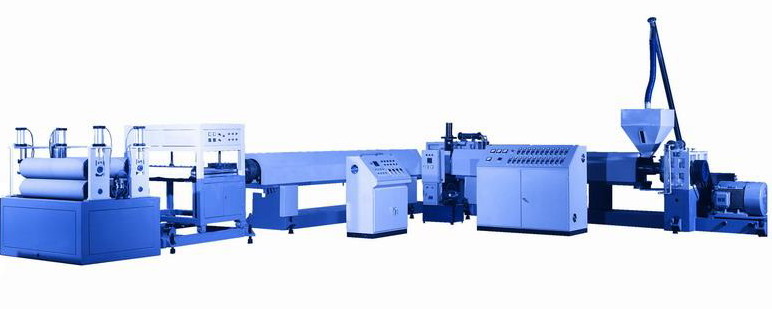
In the XPS process, polystyrene pellets, like those used to produce rigid sheet for thermoforming, are melted and blended in a regular tandem extrusion system. The extruders pump the melted material through a flat die after the foaming agent (usually based on CO2 or Hydrofluorocarbons - HFC) is injected and homogenized in the primary extruder, the polymer is extruded into secondary extruder for further homogernization and lower temperature. The foaming effect occurs as a result of the change in pressure once the polymer starts exiting the die. It is controlled as the extrudate or hot material expands between adjustable calibrating plates set to the final required thickness. Located after the plates are a train of rollers also helping to control the growth and therefore the thickness while transporting the material forward towards the finishing stations. Quality control measurements for flatness and thickness are performed before the boards are finished. The foamed product must cool and mature before it is ready for the finishing operation.
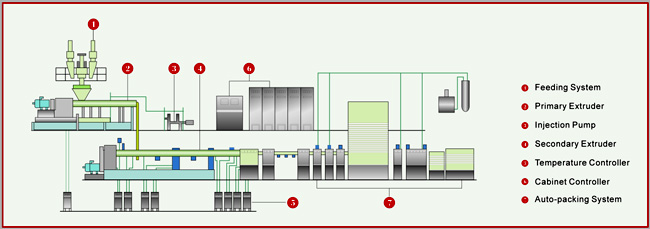
|